11 - Wing insulation for frost-protected shallow footers
Bermed foundation walls and frost-protected shallow foundations are best designed with perimeter wing insulation and waterproofing. The high thermal mass (HTM) home pictured throughout our website was bermed to help it stay sustainable through our long and harsh Rocky Mountain winters, but more importantly... the property was already sloping to the south. In most climates, an underground home is simply an aesthetic choice, not a sustainable design necessity. Berming is certainly not cost-effective on a flat property. Above-ground HTMs with shallow footer wing insulation will still always function worlds better passively than any conventional stick-frame or High-R home design.
The Underground Space Center at the University of Minnesota published excellent research in the late 70's and early 80's pointing to the fact that horizontal 'wing' insulation was preferable to vertical foundation wall insulation. Wing insulation was shown to keep the earth near foundation walls dry, greatly increasing the insulation's efficiency. Expanding greatly upon this concept, John Hait published Passive Annual Heat Storage (PAHS) in 1983. This work was dedicated to a basic concept, ignored by too many architects: keep the ground under and around foundation dry and it will retain energy better. Water transference problems aside and the classic wet, moldy basement, leaving uninsulated foundation walls in direct contact with wet earth is a huge, senseless energy loss. A giant thermal heat sink. Frost-protected shallow foundations with horizontal wing insulation protect the area under and around footers, allowing for a lower foundation 'frostwall' depth, making it perfectly suited for slab on grade, monolithic slab construction. This wing insulation technique has been standard practice since the 1950s in cold-climate Scandinavian countries.
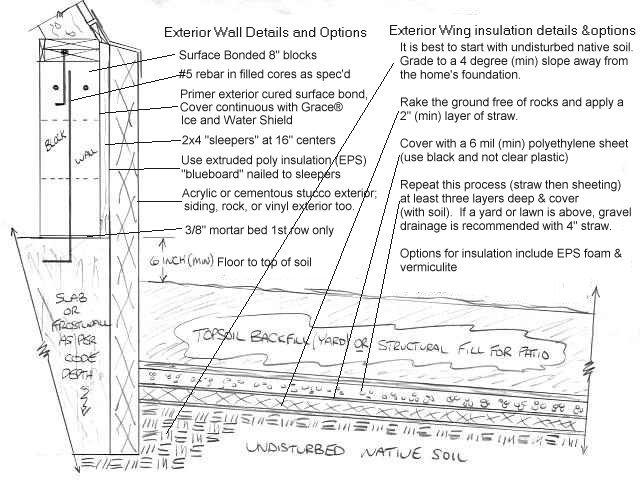
One of the most important design factors for sustainable, high thermal mass (HTM) construction is frost-protected shallow foundation wing insulation around the perimeter. As the shallow footer monolithic slab sketch above outlines, we stress the need for waterproofing and insulating up to a 20 foot perimeter around an HTM. Multiple layers of insulation or straw and EPEM or poly sheeting are recommended to avoid the chance of a single layer leaking and soaking the soil underneath. Should your site and/or budget dictate less than twenty feet of wing insulation, 8 feet is the minimum for an HTM to effectively store energy (like a battery) in the dry perimeter soil. With conventional stick-frame home foundations, as little as 2 feet or 4 feet of perimeter wing insulation will make a very noticeable difference in both heating and cooling efficiency. Wet earth in contact with any foundation will act as a constant heat sink, pulling energy away from your home. Sheets of foam board insulation are 2 feet and 4 feet wide by 8 feet long. When purchased from a wholesale distributor, a 'full bunk' is one pallet that is 8 foot tall by 4 foot by 8 foot. Ignore the per-piece price you see at building centers when estimating projects.
Optimal wing insulation installation is multiple layers of EPDM sheeting with foam board insulation between each layer. Black poly sheeting is much more economical than EPDM, but more prone to punctures, thus the greater need for multiple layers. Foam board insulation is optimal, but thick layers of straw are more economical. In addition to insulation value, the material between layers of black poly sheeting functions to prevent whatever punctures one layer from puncturing the next layer. At least three layers being optimal. Primary objective with wing insulation is to keep the ground underneath dry and able to store energy. Insulation R value is a secondary, but still very important concern if you have the money in your budget. Take care to not expose any thermal mass (exterior wall or foundation) to allow your wing insulation to function properly.
Roof runoff must be gathered and directed well away from the foundation. Moisture under and around your foundation creates an amazing heat sink that results in a lot of energy loss during both the heating and cooling seasons. Connect your roof gutters to underground pipes and take all of the roof runoff water at least 20 feet away from the foundation. If you have a flat lot, dispose of the water in underground drywell leach pits. French drains should be placed along the far edge of the wing insulation to direct ground runoff even further away from the foundation. The layers of poly sheeting should terminate by lining the 'ditch' of French drain to further protect soil underneath the wing insulation from being saturated. This is an especially important detail when installing minimal wing insulation. Topsoil above wing insulation is one foot minimum or go with a xeriscaping design with sand, rocks and stone. You can adjust this depth as needed to fit the site and the availability of backfill. We suggest one foot as a minimum since that is the least amount of soil necessary to sustain a grass yard.
HTMs do not employ any exotic building materials or methods. Construction details are common commercial, if anything. Like any block or concrete wall, electrical wiring is best in conduit within the wall. Knockouts can be made in block for outlets and switches or 'formed out' with poured-in-place walls. Plumbing usually takes advantage of chaseways above and 'wet walls' within the floorplan that are framed out. A single story, bermed, concrete block home is the easiest to build and the most efficient passive solar design for many reasons. The key to a single story HTM's often total sustainability is having the floor grounded directly to the incredibly large heat and cooling energy storage mass that the Earth underneath provides. This is the main reason why a two story home is inherently not as sustainable. Two story homes are HTM hybrids and will always need some type of mechanical heating and cooling system to service the floor above. And they're more technically difficult to build with special skills needed to build a two story home that the average homeowner-builder does not possess.
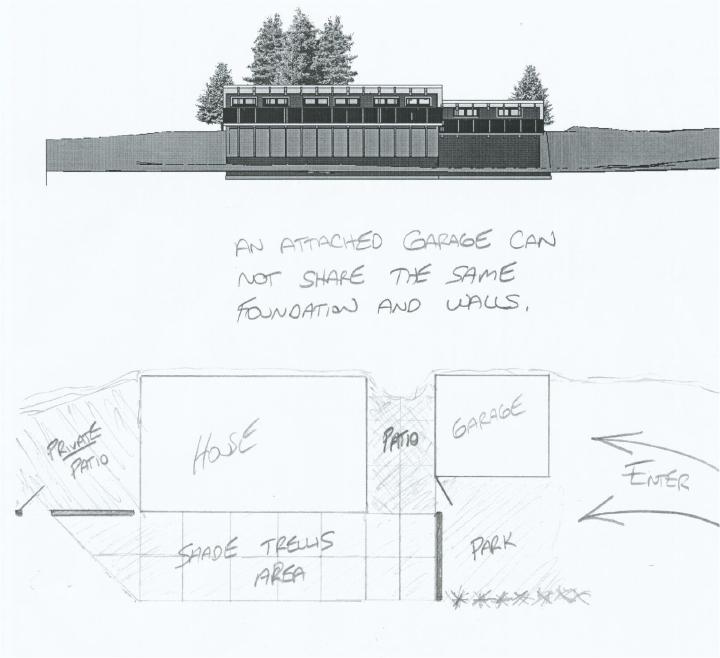
If a key interest is being energy independent, never build an attached garage with any type of home where the home and garage share a door. When the two structures share concrete footers/foundation/walls, energy flows way too easily and the garage constantly drains heating/cooling from the home. Thermally separating walls and foundation by heavily insulating underneath garage floor and between the two structures helps, but the physics works against you. There is a finite amount of passive solar gain potential - why use stored energy resources to indirectly heat/cool the garage and ground around it? We always recommend detaching the garage by at least 12 feet, preferably 20 feet, or more from the home. The integrity of your HTM home's wing insulation is key to thermal mass performance. Allowing energy to be drained off and escape through garage foundation is simply not sustainable. A covered breezeway between the two structures is very common design element to span the gap. These breezeways can be enclosed against the weather as a covered patio, adding to the integrity of the wing insulation and keeping the ground underneath warm and dry. A greater separation of public and private areas goes along with stretching the layout with a breezeway. And, the cost of building the garage portion is greatly reduced.
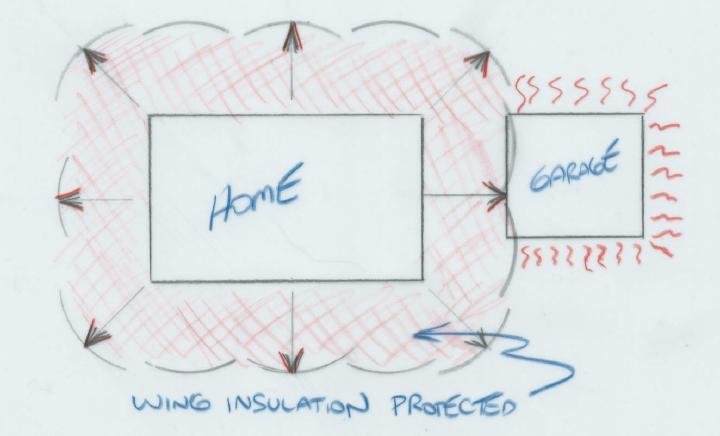
The drawing below, outlines a conventional poured-in-place frostwall foundation footer design. You can build an HTM with poured-in-place walls - it just requires special equipment and is more technically difficult the first time than stacking blocks. Concrete pours are more common from local contractors. The main advantage of dry stack block construction is its ease by the average homeowner builder and their friends. Putting up your own walls will save lots of money and make it a more personal project. When labor amounts to two-thirds of a home's total cost, it is an important consideration.
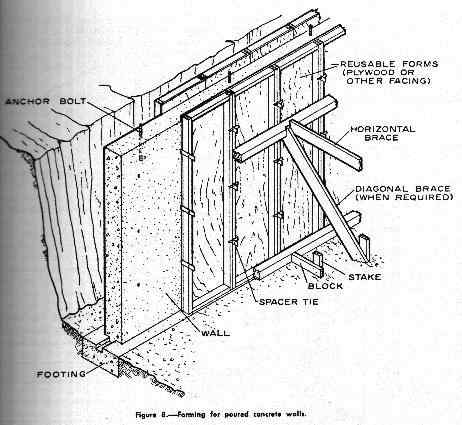
Some basic building terminology to understand:
The Uniform Building Code (UBC) is regionally modified to prevent frost heaval of your foundation walls. In the Colorado high country, the top of backfill (finish grade) extends a minimum of forty inches from the exterior finish grade (your yard surface) to the bottom of the footing (footer). When floor joists run across the top of a short frostwall, it's called a crawlspace. When you pour a frostwall tall enough to allow headroom (7'6" minimum), it's a basement. If the basement floor has a door that leads directly outside (no steps up) it's a slab-on-grade walkout basement. Slab-on-grade construction refers to pouring the concrete floor (slab) directly on the ground (grade). In the picture above, the floor slab will be poured directly on the top of footer elevation. You'll find it very handy to know the vernacular when talking with builders and architects.
With any foundation design, some keys during initial excavation:
* excavate EVERYTHING at the same time NOW and you will save thousands
* dig the septic system, lay in the well line, and grade the driveway now, not later
* strip all topsoil from foundation to ~20 foot perimeter and slope for wing insulation
* mix compost and peat moss into some of that topsoil to use atop wing insulation
* arrange piles of well-separated fill material, topsoil, and your amended 'potting soil'
Surface bonding cement SBC dry stack concrete masonry unit CMU block wall and monolithic foundation details are typical and common to any size building, but will vary depending upon size of structure, soil and site conditions, and local building codes requirements. Conservative engineering practice is to design SBC wall reinforcement (rebar) in the same grid pattern as a mortared block wall, given site, soil, and foundation variables. In HTM construction, standard practice is to fill all cores. No hollow cores in an HTM. Non-structural cores can be filled with sand or similar. But in practice, if you are 'shooting cores' with a pumper truck, it is sensible to just go ahead and pour all cores with concrete 'grout' while you have the machinery on site. We no longer provide construction, consultation, or engineering services and any information presented on this website is for 'entertainment purposes only'. Site, soil, and local code requirements are only the first of many unknown variables. We do not warrant information for any errors or omissions. Plans are not presented as construction ready. Local engineering approval must always be obtained first, before building. Click on drawing for printable Adobe .pdf file.
The roof structure, cmu rebar pattern, and backfill depth dictate ultimate wall engineering design. While possible to avoid interior perpendicular walls and counterforts entirely, it is common practice to have one every ~18 foot when the roof structure does not provide adequate stability. Placed perpendicular, roof beams act as retaining. Placed in other direction (parallel with wall) roof beams provide no wall support. Then the interior perpendicular walls both retain and provide bearing for parallel roof beams. Thus the ~18 foot mark for allowing 20 foot beams to span. Using roof trusses instead of beams has much the same, but lesser retaining effect, but only when opposite wall provides anchor for far end of truss. Sometimes you see short 'stub' block walls (counterforts) used to retain, with wood frame walls extended past counterforts on interior. Boils down to whether exterior wall is retaining backfill against structure.
Truly sustainable HTM passive solar home designs require a holistic approach, incorporating all core aspects for non-electric passively independent success. Picking and choosing HTM design components based solely on aesthetics will negatively affect passive solar function. Form follows function for best performance, economy, optimal health and personal comfort. We trust any hybrid HTM will function much better than a conventional home, but dropping a critical design element such as wing insulation or not collecting 'excess' solar energy will diminish overall passive solar performance. Our free HTM guidebook is maintained online for high thermal mass, sustainable, zero-energy, passive solar, green home building construction and design research. However, The Natural Home is not currently providing any paid engineering services or architectural design work. We cannot offer any local engineer or contractor trade referrals, other than noting stick-frame residential builders are rarely as HTM competent as commercial construction specialists. Best wishes for your project.
HTM Passive Solar eBook – Table of Contents
- introduction to high thermal mass pragmatic design, low-tech functions, and materials
- photo gallery is packed with images, commentary, and our free HTM Home Tour video
- dry stack surface bonding cement construction photos and some block layout sketches
- floor plans features several functional basic layouts and commentary on design choice
- roof detail chapter with T&G plank-style vented roof decking atop log purlin joist beams
- sun screens critical passive solar design component to create favorable micro-climates
- heat storage fiberglass water tanks are a low-tech way to moderate temperature swings
- earth tubing is simple passive technique to temper a household’s fresh air return intake
- solar orientation isn’t critical since HTM designs excel in hot or cold climates anywhere
- exterior fascia SBC coatings over EPS foam board insulation and sloped glazing details
- wing insulation and shallow footer, frost-protected perimeter foundation design choices
- planter beds are a central, functional component of greenhouse-style HTM construction
- links page is filled with a helpful selection of research references and relevant websites